The Problem: Denest, label and lid 3 pail sizes while improving throughput and minimizing footprint.
When a major American manufacturer of sealants and adhesives decided to invest in new automation equipment, Wrabacon Inc. was asked to create a proposal for the company’s pail denesters, lid denesters, lid presses, and pail turners.
What is Denesting? For the uninitiated, a pail (or lid) denester automates the pulling-apart of buckets or pails so that they can then be automatically placed into a system where they are filled, labeled, and sealed shut. Prior to installing a custom solution by Wrabacon, the facility’s only automation took place when pails were actually filled, and it could only be done as fast as an employee could manually move each bucket to and from the filling area. Denesting the pails, lidding them, and labeling them was all done by hand – which posed problems for ergonomics, production rate, and efficiency. By introducing a more automated solution, our customer could finally realize the fast, predictable, and effective throughput that would allow them to grow.
What Was the Need?
A system that could quickly and efficiently automate a pail filling line, while accommodating 3 pail sizes with their own fill rates, label and lid sizes.
It Counts to Be Creative
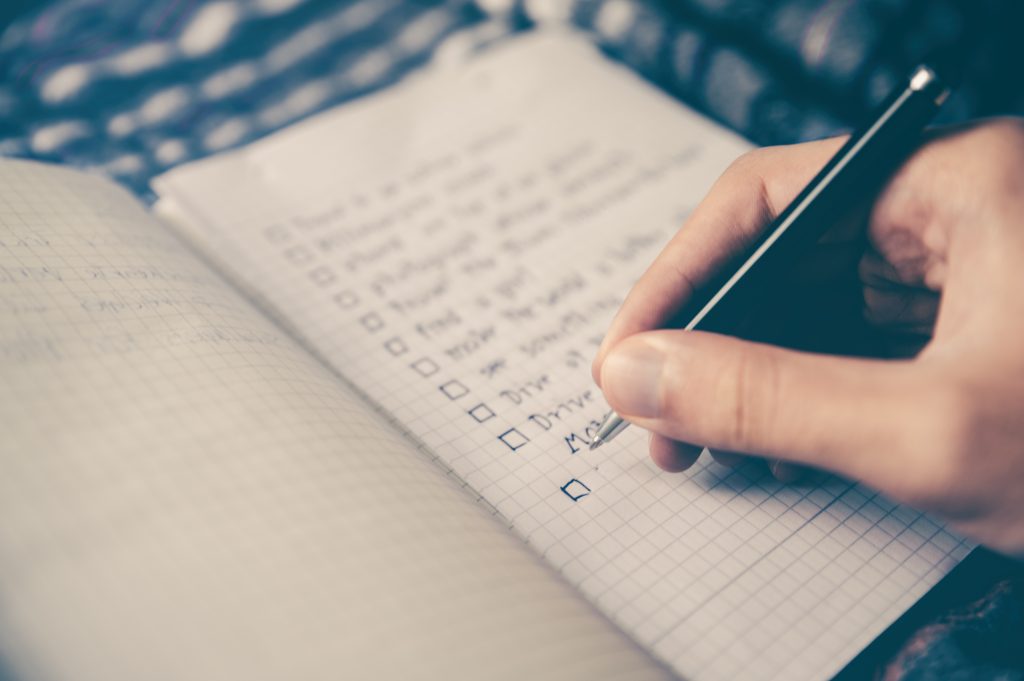
After reviewing several other vendors for this equipment, the client chose Wrabacon’s proposed solution, not because our machine was fancier, but because it was tailor-made to meet their specific goals: a small foot print, and a high ROI. This was done by carefully considering their space and application.
To meet our client’s need, our creative automation experts went to work to carefully study the application, the environment, and the product at hand.
At Wrabacon, this stage in the process is critical. Not only does it give our engineers the opportunity to fully understand our client’s facility and process – but it enables our team to create a truly custom automation solution that accounts for the many possible variables at play with each application or environment.
The Solution: Wrabacon’s Denester
Reliable Throughput, Minimal Footprint
For our customer, the goal was to handle 3 separate container sizes, while ensuring both a small footprint and a high degree of reliability. Does that mean 1 complex system for all 3 sizes to save space? Or a hybrid solution that’s slightly larger, but less intricate and more reliable? It’s questions like these that our team tackles for every custom system.
Every creative automation project is a balancing act. Too much adjustability and size differential can cause problems with throughput and reliability. Too little, and the space required for each system component can become unwieldy.
Our team worked to strike the ideal balance. By carefully considering the customer’s facility and process, we made the determination that a single machine for all 3 pail sizes just wouldn’t meet their needs without sacrificing performance, reliability, and ROI.
Instead, our system uses one denester for bailed buckets in the two largest sizes, with a separate denester for non-bailed ½ gallon buckets. After the pails are denested, they then progress to a labeling area, a filling area (pre-existing), and a lidding area. Finally, each pail exits the system after being guided down an incline conveyor and manually removed.
Throughout the process, our design remains focused on carefully guiding each pail to its destination quickly and efficiently – with numerous stops and guides to ensure reliability and control.
Labeling
Orient, Adjust, and Label Pails in 3 Different Sizes
After pails are de-nested on their respective machines, they enter the labeling area where a pneumatic gate stops each pail before a set of side-belts rotate the pail to a preset position for labeling. After labels are placed, the system will release the pail from its position and lower a pair of stop gates to let the pail continue downstream to be transferred onto the client’s filling conveyor.
Lid Denesting and Rolling
Two Systems, Multiple Sizes, Greater Efficiency
For this system, the two larger containers share a lid denester and placer while the smaller pails utilize their own lid denester and placer. With hoppers that can be loaded at any time, the operation of this system halts each pail with a stopping gate so that lids can be released from above and dropped loosely onto the container. Next, they move downstream where each lid is rolled onto the container with a series of tapered rollers. The size difference between pails dictates the only change in functionality between large lid denesters and small lid denesters – which allows the smaller denester to handle two containers at once, with a dual vertical hopper.
The Result
Space Saving Reliability at a Competitive Price
Ultimately, our entire system was designed to be a simple and efficient automation solution to separate buckets and lids, while also handling alignment for labeling and lidding. In the beginning, all denesting, labeling, and lidding was done by hand. Today, the company experiences much greater productivity and efficiency – allowing them to accurately forecast throughput and productivity while more efficiently (and competitively) providing product to customers around the world.